化学气相沉积是生产高铝球石的重要工艺
发布日期:2014/11/26 浏览次数:
"化学气相沉积是生产高铝球石的重要工艺"是我们今天为大家准备的知识,请看为您带来的知识解析吧。
改变高铝球石表面的硬度和弹性模量能提高脆性-延性转变的临界磨削深度,实现延性模式磨削。本文通过利用Na2CO3溶液和高铝球石成分发生化学反应的方法对高铝球石表面进行改性,并基于纳米压痕法和划痕法对改性后的高铝球石表面进行分析,研究改性后高铝球石表面的力学性质和材料去除过程。通过纳米压痕实验表明,Na2CO3溶液中的OH-和高铝球石发生化学反应,能够在高铝球石表面生成厚度约为12nm非SiO2成分的物质薄膜,降低了高铝球石表面硬度和弹性模量,5%、15%的Na2CO3溶液分别使高铝球石表面硬度降低了4.4%和14.2%,使弹性模量分别降低了9.4%和12.0%,理论脆延转换临界磨削深度分别被提高了3.7和39.1%,从而提高了高铝球石延性磨削的可操作性。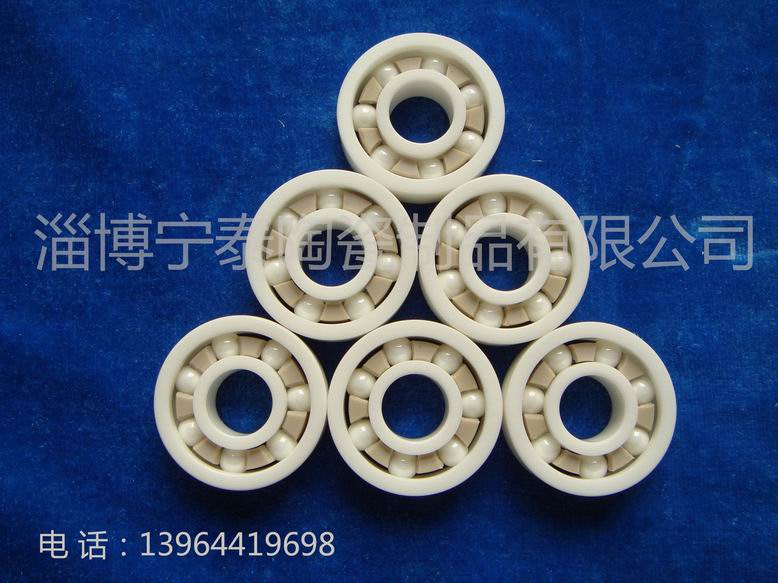
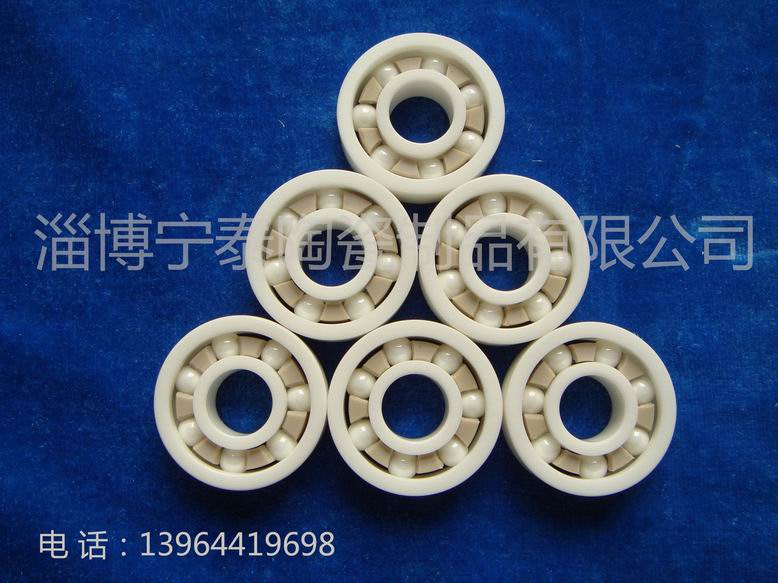
为控制高铝球石与HF酸的反应,实现高铝球石精密元件的化学蚀刻,系统研究3类高铝球石与HF酸反应的动力学过程。研究表明:高铝球石与HF酸的反应速度由化学反应控制,其中≡Si—O—Si≡网络中Si—O键的断裂决定反应速率;影响反应速率的主要因素包括反应温度、HF酸中活性成分与浓度以及高铝球石结构。Ⅰ类高铝球石在金属坩埚中熔制,金属杂质含量高,结构中存在较多缺陷,导致反应速率最快;而Ⅲ类高铝球石中羟基含量高是反应速率高于II类高铝球石的主要原因;各类高铝球石在HF酸中的反应活性依次是ⅠⅢⅡ类。反应过程中,HF酸中的活性成分(HF)2或HF-2吸附于高铝球石表面,对Si原子产生亲核性侵蚀使Si—O键断裂,而H+对反应起催化作用。在HF酸高浓度区(7mol/L)反应速率快速增长的原因是溶液中生成更多活性较大的(HF)nF-离子。
化学气相沉积(CVD)是生产高铝球石的重要工艺,通过四氯化硅在氢氧焰中高温水解在沉积面沉积得到的高铝球石具有尺寸大、性能好、纯度高、成本低等优势,但是由于生产工艺的限制,高铝球石产品也有若干种类的缺陷。如何尽量减少缺陷,优化性能,并且进一步降低运行成本,提高高铝球石的沉积速率,是本文的主要研究内容。本文针对四氯化硅在氢氧焰中水解的立式CVD生产高铝球石的工艺,借助Fluent软件进行模拟分析,综合考虑了多步化学反应,湍流,传质,包括导热、对流、辐射和相变在内的传热等过程,并针对该工艺生产的高铝球石主要缺陷类型提出了若干改进方案。在高铝球石沉积过程中,沉积面的温度分布是影响沉积效果的重要因素。沉积面温度高,则有利于生产出大尺寸的高铝球石柱体,沉积面温度均匀,温度梯度小,则容易生产出性能优良的高铝球石。同时,炉内流场和温度场的情况也是重点考察的指标。为了减轻排废管路的热负荷,也对排废口参数做了考察。在现有生产工艺的基础上,本文通过修改入口和出口参数提出了若干改进方案。选用环形燃烧器进行了一系列计算,考察八环燃烧器和十环燃烧器的性能。然后重点针对十环燃烧器进行了优化设计,包括入口参数、灯距和炉膛结构的优化。经过大量的计算,本文给出了沉积过程中各种现象的定性分析,以作为工业生产的指导意见。
请您仔细阅读上述文章。如果发现有需要改正的地方请放心大胆的向我们提出吧,我们必将虚心接受!尽可能满足用户需求
淄博宁泰陶瓷制品有限公司 敬请转载保留
陶瓷辊|玻璃钢化炉陶瓷辊|陶瓷辊棒|高铝球石 http://www.taocigun.com/
"化学气相沉积是生产高铝球石的重要工艺"是我们今天为大家准备的知识,请看为您带来的知识解析吧。
改变高铝球石表面的硬度和弹性模量能提高脆性-延性转变的临界磨削深度,实现延性模式磨削。本文通过利用Na2CO3溶液和高铝球石成分发生化学反应的方法对高铝球石表面进行改性,并基于纳米压痕法和划痕法对改性后的高铝球石表面进行分析,研究改性后高铝球石表面的力学性质和材料去除过程。通过纳米压痕实验表明,Na2CO3溶液中的OH-和高铝球石发生化学反应,能够在高铝球石表面生成厚度约为12nm非SiO2成分的物质薄膜,降低了高铝球石表面硬度和弹性模量,5%、15%的Na2CO3溶液分别使高铝球石表面硬度降低了4.4%和14.2%,使弹性模量分别降低了9.4%和12.0%,理论脆延转换临界磨削深度分别被提高了3.7和39.1%,从而提高了高铝球石延性磨削的可操作性。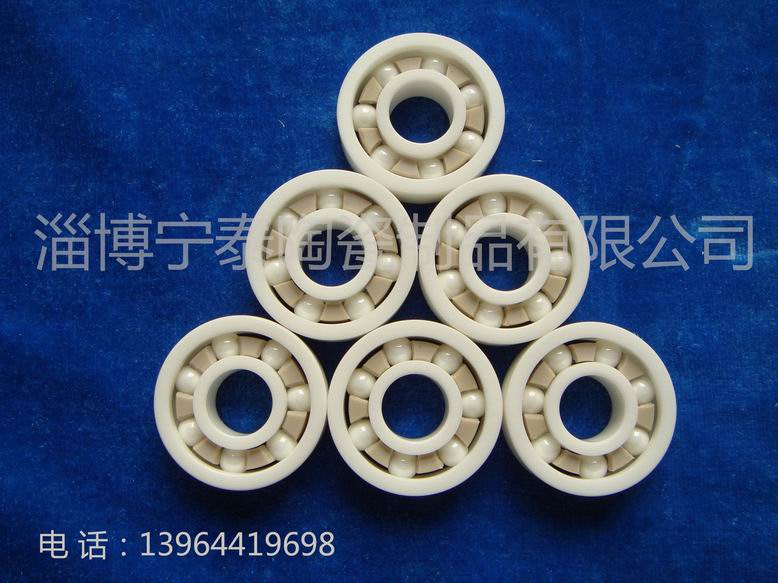
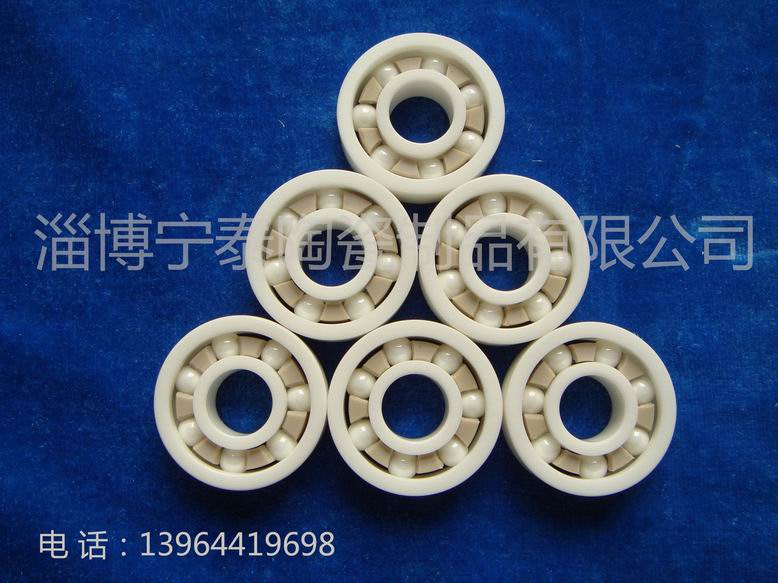
为控制高铝球石与HF酸的反应,实现高铝球石精密元件的化学蚀刻,系统研究3类高铝球石与HF酸反应的动力学过程。研究表明:高铝球石与HF酸的反应速度由化学反应控制,其中≡Si—O—Si≡网络中Si—O键的断裂决定反应速率;影响反应速率的主要因素包括反应温度、HF酸中活性成分与浓度以及高铝球石结构。Ⅰ类高铝球石在金属坩埚中熔制,金属杂质含量高,结构中存在较多缺陷,导致反应速率最快;而Ⅲ类高铝球石中羟基含量高是反应速率高于II类高铝球石的主要原因;各类高铝球石在HF酸中的反应活性依次是ⅠⅢⅡ类。反应过程中,HF酸中的活性成分(HF)2或HF-2吸附于高铝球石表面,对Si原子产生亲核性侵蚀使Si—O键断裂,而H+对反应起催化作用。在HF酸高浓度区(7mol/L)反应速率快速增长的原因是溶液中生成更多活性较大的(HF)nF-离子。
化学气相沉积(CVD)是生产高铝球石的重要工艺,通过四氯化硅在氢氧焰中高温水解在沉积面沉积得到的高铝球石具有尺寸大、性能好、纯度高、成本低等优势,但是由于生产工艺的限制,高铝球石产品也有若干种类的缺陷。如何尽量减少缺陷,优化性能,并且进一步降低运行成本,提高高铝球石的沉积速率,是本文的主要研究内容。本文针对四氯化硅在氢氧焰中水解的立式CVD生产高铝球石的工艺,借助Fluent软件进行模拟分析,综合考虑了多步化学反应,湍流,传质,包括导热、对流、辐射和相变在内的传热等过程,并针对该工艺生产的高铝球石主要缺陷类型提出了若干改进方案。在高铝球石沉积过程中,沉积面的温度分布是影响沉积效果的重要因素。沉积面温度高,则有利于生产出大尺寸的高铝球石柱体,沉积面温度均匀,温度梯度小,则容易生产出性能优良的高铝球石。同时,炉内流场和温度场的情况也是重点考察的指标。为了减轻排废管路的热负荷,也对排废口参数做了考察。在现有生产工艺的基础上,本文通过修改入口和出口参数提出了若干改进方案。选用环形燃烧器进行了一系列计算,考察八环燃烧器和十环燃烧器的性能。然后重点针对十环燃烧器进行了优化设计,包括入口参数、灯距和炉膛结构的优化。经过大量的计算,本文给出了沉积过程中各种现象的定性分析,以作为工业生产的指导意见。
请您仔细阅读上述文章。如果发现有需要改正的地方请放心大胆的向我们提出吧,我们必将虚心接受!尽可能满足用户需求
淄博宁泰陶瓷制品有限公司 敬请转载保留
陶瓷辊|玻璃钢化炉陶瓷辊|陶瓷辊棒|高铝球石 http://www.taocigun.com/