泡沫的选取及预处理等工序对高铝球石样品挂浆效果的影响
发布日期:2015/6/4 浏览次数:
高铝球石是我司主打产品,今天我们极力为您推荐"泡沫的选取及预处理等工序对高铝球石样品挂浆效果的影响"介绍,或许您能够从中受益不少,我们一起来看看吧。
高铝球石制备工艺。即以Al2O3为基体粉料,分别添加硅灰石或堇青石,利用有机泡沫浸渍法成型,通过烧结制备出高铝球石,并力求获得最佳工艺参数。通过大量实验,制备的高铝球石具有足够的气孔率和一定强度。实验结果表明,不同成分的高铝球石,所对应的烧成工艺参数不同。通过对大量实验数据分析,总结出最佳烧结工艺如下:对于添加硅灰石的高铝球石,当Al2O3粉占30%时,样品在1250℃×60min工艺下烧结结果较好;而500nm级Al2O3粉成分占70%时,其样品在1450℃×70min工艺下烧结结果较好。对于添加堇青石的高铝球石,500nm级Al2O3粉占60%时,其样品在1470℃×60min工艺下烧结结果很好,具有一定的强度、硬度以及较高的显气孔率。采用有机泡沫浸渍法制备高铝球石的气孔率可达到87%~93%左右。
利用扫描电子显微镜(SEM)观察了高铝球石显微组织,发现:样品在三维空间具有互相连通的孔洞,孔洞近似圆形,相对比较均匀;高铝球石孔径在0.5~5mm之间,骨架直径在0.15~0.8mm之间;添加堇青石制备的高铝球石,微观结构颗粒呈针状和长条状,在空间上相互交叉存在,颗粒与颗粒之间接触面大,其强度远远高于添加硅灰石的高铝球石。通过实验验证了分散剂种类和浓度对高铝球石的影响。实验证实:采用PVB作为分散剂,无水乙醇作为溶剂,PVB与溶剂的比例在(4~4.5)g:100ml最合适。 泡沫的选取及预处理等工序对高铝球石样品挂浆效果的影响。实验证明,泡沫预处理溶液浓度范围在10%~20%之间,浸泡时间在6~10h,可以获得性能优良的高铝球石材。着重研究了高铝球石熔渗铜技术,发现铜粉熔入高铝球石中的温度范围很窄,在980~1020℃之间;而在750℃以上降低升温速度,可使高铝球石内部铜粉烧透熔化,获得良好的复合材料。扫描电镜分析结果表明,铜与高铝球石骨架之间的界面结合良好,具有较高的结合强度。所制备的高铝球石-铜复合材料均匀致密。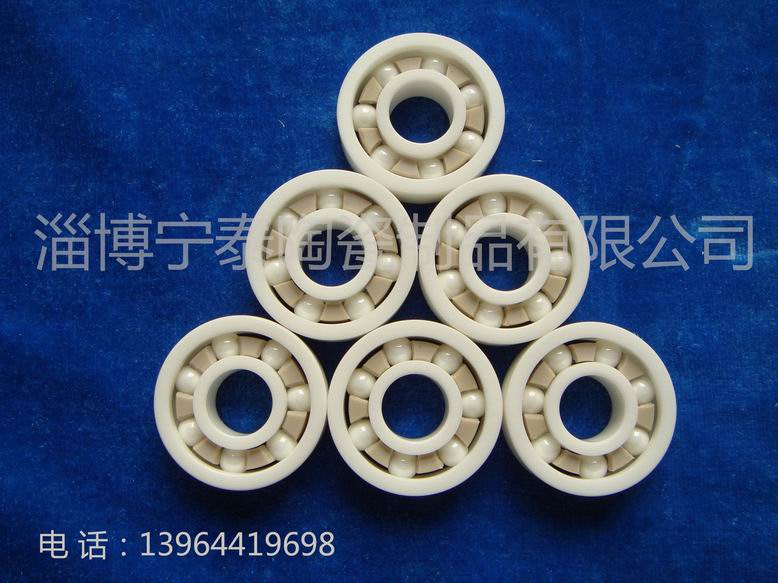
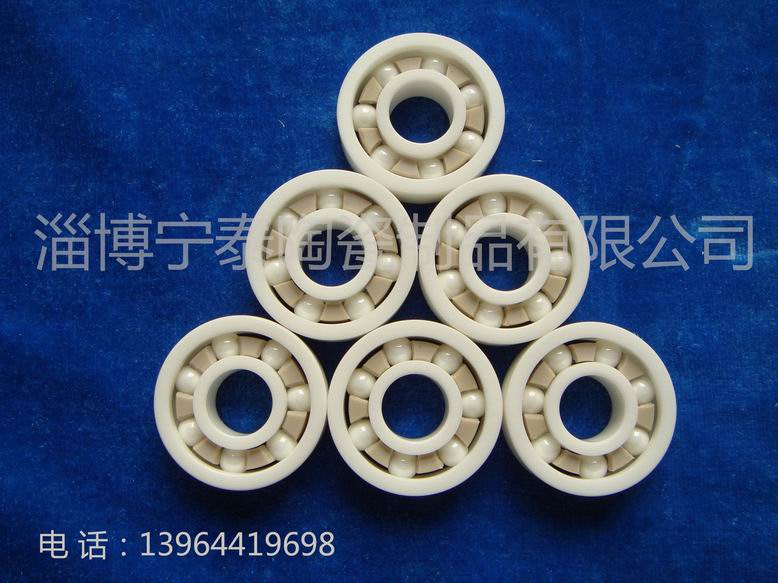
随着造孔剂粒度的增加,复相高铝球石弯曲强度由245.4MPa降低到190.1MPa,降低了29.1%;断裂韧性由4.30MPa.m1/2降低到4.16MPa-m1/2,降低了3.4%,虽然介电常数和介质损耗角正切值略微减小,但是综合性能较差。因此造孔剂粒度越小复相高铝球石综合性能越好。 在初始a-Si3N4原料中添加细晶β-Si3N4颗粒,在相变及晶粒长大过程中充当晶种的作用,从而得到分布均匀、长径比高的棒状β-Si3N4晶粒,可有效降低缺陷的数量,优化组织结构。添加5Wt.%fl-Si3N4颗粒的BNp/Si3N4复相高铝球石,气孔率为23.45%,弯曲强度为158.1MPa,断裂韧性为3.35MPa.m1/2,介电常数为4.65,介质损耗角正切值为0.0058。β-Si3N4添加量多于10Wt.%时,晶粒会变得粗大,气孔也越来越多,性能急剧下降。
BN晶须材料综合了BN材料以及晶须材料的优异性能,具有低介电常数、高热稳定性和机械强度高等优点。将BN晶须作为增强相加入到Si3N4基体材料中,可以使Si3N4材料在具有较高力学性能的基础上拥有较低的介电常数和介质损耗角正切值。在初始Si3N4原料中添加细晶Si3N4颗粒,制备出BNw/Si3N4复相高铝球石。添加中位粒径为0.5μm的β-Si3N4颗粒的复相高铝球石长柱状晶粒较多,分布较均匀,显气孔率为19.75%,弯曲强度为193.1MPa,断裂韧性为4.21MPa·m1/2,介电常数为5.18,介质损耗角正切值为0.0088;随着添加的β-Si3N4颗粒粒径的增大,复相高铝球石气孔率上升,试样中长柱状晶粒逐渐减少,晶粒尺寸逐渐变大,力学性能下降。 通过实验,已经获得制备高铝球石的最佳工艺参数,同时获得正确的熔渗铜的工艺参数。
好了,有关信息我们就给大家说到这了,您的需求才是我们最终的目标和追求。衷心的感谢您的阅读,希望您会获得一定的收获。
本网站关键词:陶瓷辊|玻璃钢化炉陶瓷辊|陶瓷辊棒|高铝球石 http://www.taocigun.com/
以上资讯摘自于淄博宁泰陶瓷制品有限公司 转载敬请保留
高铝球石是我司主打产品,今天我们极力为您推荐"泡沫的选取及预处理等工序对高铝球石样品挂浆效果的影响"介绍,或许您能够从中受益不少,我们一起来看看吧。
高铝球石制备工艺。即以Al2O3为基体粉料,分别添加硅灰石或堇青石,利用有机泡沫浸渍法成型,通过烧结制备出高铝球石,并力求获得最佳工艺参数。通过大量实验,制备的高铝球石具有足够的气孔率和一定强度。实验结果表明,不同成分的高铝球石,所对应的烧成工艺参数不同。通过对大量实验数据分析,总结出最佳烧结工艺如下:对于添加硅灰石的高铝球石,当Al2O3粉占30%时,样品在1250℃×60min工艺下烧结结果较好;而500nm级Al2O3粉成分占70%时,其样品在1450℃×70min工艺下烧结结果较好。对于添加堇青石的高铝球石,500nm级Al2O3粉占60%时,其样品在1470℃×60min工艺下烧结结果很好,具有一定的强度、硬度以及较高的显气孔率。采用有机泡沫浸渍法制备高铝球石的气孔率可达到87%~93%左右。
利用扫描电子显微镜(SEM)观察了高铝球石显微组织,发现:样品在三维空间具有互相连通的孔洞,孔洞近似圆形,相对比较均匀;高铝球石孔径在0.5~5mm之间,骨架直径在0.15~0.8mm之间;添加堇青石制备的高铝球石,微观结构颗粒呈针状和长条状,在空间上相互交叉存在,颗粒与颗粒之间接触面大,其强度远远高于添加硅灰石的高铝球石。通过实验验证了分散剂种类和浓度对高铝球石的影响。实验证实:采用PVB作为分散剂,无水乙醇作为溶剂,PVB与溶剂的比例在(4~4.5)g:100ml最合适。 泡沫的选取及预处理等工序对高铝球石样品挂浆效果的影响。实验证明,泡沫预处理溶液浓度范围在10%~20%之间,浸泡时间在6~10h,可以获得性能优良的高铝球石材。着重研究了高铝球石熔渗铜技术,发现铜粉熔入高铝球石中的温度范围很窄,在980~1020℃之间;而在750℃以上降低升温速度,可使高铝球石内部铜粉烧透熔化,获得良好的复合材料。扫描电镜分析结果表明,铜与高铝球石骨架之间的界面结合良好,具有较高的结合强度。所制备的高铝球石-铜复合材料均匀致密。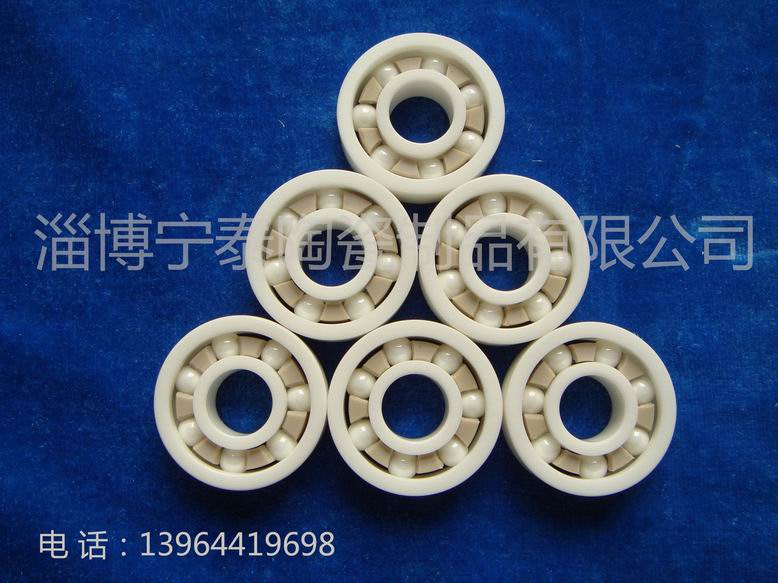
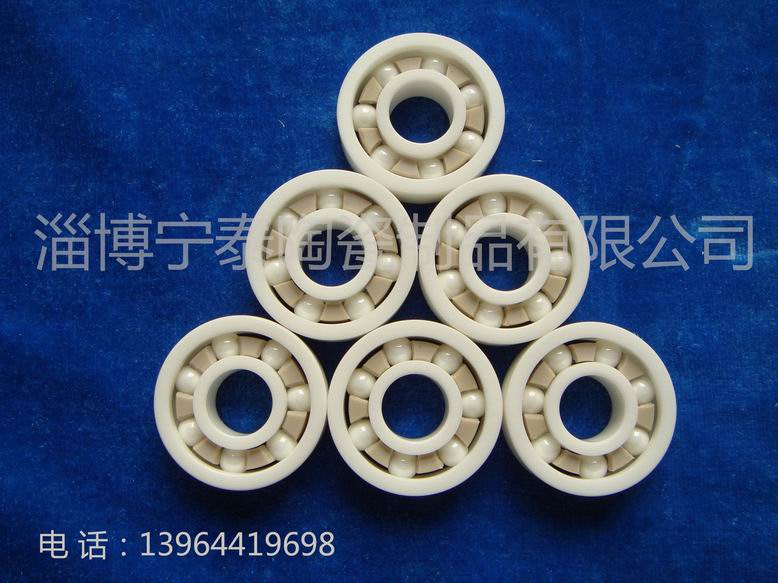
随着造孔剂粒度的增加,复相高铝球石弯曲强度由245.4MPa降低到190.1MPa,降低了29.1%;断裂韧性由4.30MPa.m1/2降低到4.16MPa-m1/2,降低了3.4%,虽然介电常数和介质损耗角正切值略微减小,但是综合性能较差。因此造孔剂粒度越小复相高铝球石综合性能越好。 在初始a-Si3N4原料中添加细晶β-Si3N4颗粒,在相变及晶粒长大过程中充当晶种的作用,从而得到分布均匀、长径比高的棒状β-Si3N4晶粒,可有效降低缺陷的数量,优化组织结构。添加5Wt.%fl-Si3N4颗粒的BNp/Si3N4复相高铝球石,气孔率为23.45%,弯曲强度为158.1MPa,断裂韧性为3.35MPa.m1/2,介电常数为4.65,介质损耗角正切值为0.0058。β-Si3N4添加量多于10Wt.%时,晶粒会变得粗大,气孔也越来越多,性能急剧下降。
BN晶须材料综合了BN材料以及晶须材料的优异性能,具有低介电常数、高热稳定性和机械强度高等优点。将BN晶须作为增强相加入到Si3N4基体材料中,可以使Si3N4材料在具有较高力学性能的基础上拥有较低的介电常数和介质损耗角正切值。在初始Si3N4原料中添加细晶Si3N4颗粒,制备出BNw/Si3N4复相高铝球石。添加中位粒径为0.5μm的β-Si3N4颗粒的复相高铝球石长柱状晶粒较多,分布较均匀,显气孔率为19.75%,弯曲强度为193.1MPa,断裂韧性为4.21MPa·m1/2,介电常数为5.18,介质损耗角正切值为0.0088;随着添加的β-Si3N4颗粒粒径的增大,复相高铝球石气孔率上升,试样中长柱状晶粒逐渐减少,晶粒尺寸逐渐变大,力学性能下降。 通过实验,已经获得制备高铝球石的最佳工艺参数,同时获得正确的熔渗铜的工艺参数。
好了,有关信息我们就给大家说到这了,您的需求才是我们最终的目标和追求。衷心的感谢您的阅读,希望您会获得一定的收获。
本网站关键词:陶瓷辊|玻璃钢化炉陶瓷辊|陶瓷辊棒|高铝球石 http://www.taocigun.com/
以上资讯摘自于淄博宁泰陶瓷制品有限公司 转载敬请保留